Electricity is one of the indispensable energy sources in modern life, and it is essential for the rapid development of the industry. Oil refineries, power plants, semiconductor factories, etc. that work in high-risk areas, as long as they use high-voltage electricity, need Wear electrical PPE as the first line of defenses in case of any accidents.
Different types of electrical hazards
- Electric shock: This is the most common type of electrical hazard and occurs when an individual comes into contact with a live electrical conductor. The severity of an electric shock depends on the amount of current flowing through the body. It can range from minor tingling sensations to serious injury or even death.
- Arc flash: An arc flash occurs when a high-energy electrical discharge generates an explosion of heat and light. This can happen while operating high-voltage electrical equipment and the resulting arc flash can lead to severe burns, blindness, or even death.
- Electromagnetic radiation: This type of hazard is less well-known than others. However, it can still pose a risk to individuals who work with electrical equipment. Electromagnetic radiation can cause health problems, such as headaches, dizziness, and nausea. Long-term exposure can lead to more serious health issues.
- Fire and explosions: Electrical fires and explosions can occur when electrical equipment overheats or malfunctions, causing sparks or short circuits that ignite flammable materials. These fires and explosions can cause significant property damage, injuries, and even fatalities.
In addition to possessing professional technical knowledge, regular education, and training, and regularly maintaining equipment, high-risk work areas require electrical personal protective equipment (PPE). Electrical PPE protects workers who are working with or close to live circuits against electrical hazards. Electrical PPE is critical to keeping workers safe, as it protects against electrocution, burns, and other electrical hazards.
Factors to Consider When Choosing Electrical PPE
Work Environment
The type of work environment can significantly impact the choice of Electrical PPE. Factors such as temperature, humidity, and the presence of flammable or explosive materials should be considered. For example, if the work environment is hot and humid, lightweight and breathable PPE may be necessary to prevent heat stress. If there are flammable or explosive materials present, antistatic or conductive PPE may be required to reduce the risk of sparks or static electricity.
Job duties and tasks
The type of job duties and tasks performed will also influence the choice of electrical PPE. You should consider factors such as the level of electrical hazards present, the type of equipment being worked on, and the proximity to electrical sources.
For example, suppose the work involves working on high-voltage equipment. In that case, PPE with a high arc rating may be necessary to protect against arc flash hazards. If the job involves working in tight spaces, lightweight PPE that allows for freedom of movement may be necessary.
Level of electrical hazards
There are four levels of electrical hazards based on the amount of voltage present and the level of protection required. These levels are defined by the National Fire Protection Association (NFPA) in NFPA 70E, the Standard for Electrical Safety in workplaces, and help to identify the right PPE used for each electrical work.
- Hazard Risk Category (HRC) 0: This level applies to work with low-voltage equipment (below 50 volts) and does not require any PPE beyond regular work clothing.
- HRC 1: This level applies to work with equipment operating at 50-300 volts and requires using Arc-rated clothing and hearing protection.
- HRC 2: This level applies to work with equipment operating at 300-600 volts and requires using arc flash fabric protection, hearing protection, and safety glasses or goggles.
- HRC 3 and HRC 4: These levels apply to work with equipment operating at higher voltages (above 600 volts). HRC 3 requires using Arc-rated clothing, hearing protection, safety glasses or goggles, and a face shield. HRC 4 requires all the PPE required for HRC 3, plus a suit hood or a helmet designed for arc flash protection.
It is important to assess the level of electrical hazards in the workplace and provide the appropriate PPE and training to employees to protect them from electrical hazards.
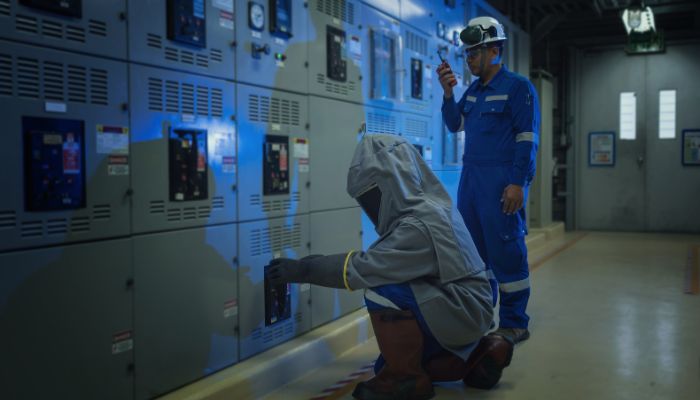
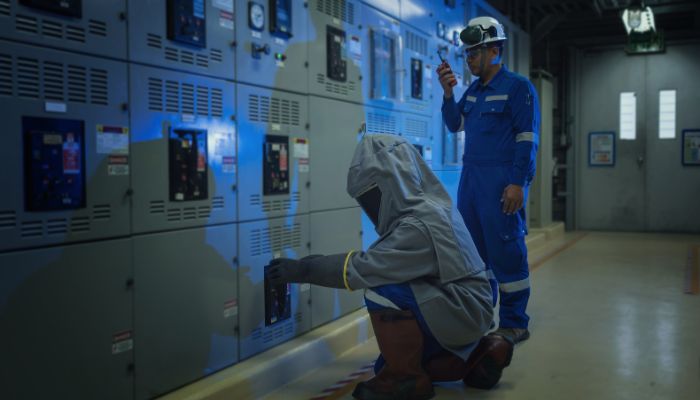
Types of Electrical Safety Clothing Equipment
Employees working in areas with potential electrical hazards must be equipped and use electrical protective equipment appropriate for the specific part of the body being protected and the job being performed. Electrical personal protective equipment (PPE) covers from head to toe, and the most important thing is to protect the first time when an accident occurs, with a few seconds to react and protect to ensure that there is a chance of escape.
1. Insulating gloves
The material is mostly nylon/rubber/leather, which is electrically insulated.
2. Dielectric boots
Dielectric boots are electrical hazard-resistant boots made of insulating materials such as rubber, neoprene, or polyurethane. It can prevent the current from grounding, and the current flows through the boots to protect the wearer from electrical hazards. If the event of an accident, high-voltage currents can stop the heart or cause fatal burns. Isolation of the feet from the ground can reduce injuries. Industries with a high risk of electrical shock commonly use these boots in electrical work and power generation.
3. Conductive footwear
Conductive footwear, on the other hand, is designed to provide a path for electrical current to flow through the shoes, effectively grounding the wearer. This type of footwear is common in industries where static electricity is a concern, such as in electronics manufacturing, clean rooms, or explosive environments. Manufacturers make conductive footwear with materials such as carbon, metal, or other conductive materials.
4. Arc flash suits & Flame-resistant clothing
Designers create arc flash suits to safeguard workers from the intense heat and energy emitted during an electrical arc flash. Arc flash usually takes less than one second, and the temperature can reach 10,000 degrees. It is one of the most dangerous industrial safety issues. Materials used in this type of clothing are designed to self-extinguish when exposed to flames, which helps to prevent or minimize burn injuries. The specific type of PPE required will depend on the nature of the hazards present in the workplace and the level of protection that is
5. Voltage-rated tools
Voltage-rated tools are electrical tools designed and tested to withstand specific voltage levels. These tools are often used in electrical work, power generation, and other industries with a high risk of electrical shock. Voltage-rated tools are designed to protect the user from electrical shock by preventing the flow of electrical current through the tool and into the user's body. These tools are rated for specific voltage levels to ensure they meet safety standards.
6. Electrical safety glasses
Electrical safety glasses protect the eyes from electrical hazards such as arcs, flashes, and stray currents and have additional features such as side shields and UV protection.
7. Electrical protective helmets
Electrical safety glasses protect the eyes from electrical hazards such as arcs, flashes, and stray currents and have additional features such as side shields and UV protection.
Choosing the Right Material for Electrical PPE Clothing
Flame-retardant fabrics can be divided into flame retardant treated fabrics and Inherent flame-resistant fabric.
Their content is very different. Flame retardant treated fabrics account for 60%-70% of the European and American markets, most of which are Cotton and Rayon, and the effect is achieved through chemical treatment. The fabric can absorb moisture and feel softer, but it requires safety control of chemicals because flame retardant agents are very poisonous. Flame retardant treated fabrics are produced by applying a chemical finishing to a fiber or the fabric to reduce its flammability. The flame retardant treatment chemicals are “activated” by intense heat, producing char and gases that inhibit combustion for a certain time.
Inherent flame-resistant fabrics are made of fibers whose inherent properties make them naturally flame retardant without chemical treatment. Inherently flame resistant fabrics are mostly made from Meta-aramid, Para-aramid, Modacrylic, FR-Rayon and Oxidized PAN Fiber (OPF).
Material | Characteristic | Hand feeling | LOI |
---|---|---|---|
Cotton | Natural fibers are easy to absorb moisture, are breathable, and provide comfort. | Soft and skin-friendly. | 18-19 |
FR-Rayon | With good dyeability, natural fibers are easy to wick and breathe. | Lightweight, Soft and skin-friendly. | 28 |
Meta-aramid | Chemical acid and alkali resistance, good wear resistance. | Soft. | 28-32 |
Para-aramid | Anti-cutting, most bulletproof vests are made of this material. | Hard. | 26-29 |
Modacrylic | Easy to dye and finish. It has the characteristics of anti-mildew, anti-UV, and chemical resistance. | Good softness and gloss, feel fluffy. | 28-33 |
Oxidized Pan Fiber(OPF) | It has very high thermal stability, maintains elasticity and durability, does not shrink when exposed to flames, and self-extinguishes. | It retains its appearance, softness, and textile properties even after exposure to open flames. | 45-60 |
Remark: LOI (The Limiting Oxygen Index) is an indicator used to evaluate the flame resistance of the fibers. The measurement method involves placing the substance to be tested in a flame chamber and measuring the minimum percentage of oxygen content that can cause the substance to burn by changing the ratio of oxygen to nitrogen in the test environment. Higher numbers indicate greater resistance to fire.
Cleaning and Maintenance of Electrical PPE
For flame-retardant work clothes cleaning, it’s better to be washed without bleach, as bleach may compromise the FR performance of flame-retardant fabrics. Proper cleaning and maintenance of electrical PPE are important to ensure that it continues providing the required protection level. Store electrical PPE in a clean, dry, and cool location. Keep the PPE away from direct sunlight, heat, and chemicals. Replace PPE that has reached the end of its useful life or has been damaged beyond repair.
Conclusion
Compared to flame-retardant-treated fabrics, inherently flame-resistant fabrics are more environment friendly due to the inherent flame retardant nature of fibers. However, due to their nature, these materials may not be easy to color during dyeing and finishing. Material weight, function, and comfort are all interrelated, and as a result, most of these fabrics are blended to achieve a balance of functional requirements in the market. It is crucial for workers to wear adequate flame-resistant protective clothing, as it provides escape time, reduces burn injuries, and increases the wearer's chances of survival.
You may also like